Introduction: What Are Composite Materials?
Composite materials are engineered materials made from two or more different substances that, when combined, exhibit properties superior to those of the individual components. They are essential in a variety of industries, including aerospace, automotive, construction, and even sports equipment. Understanding how these materials work, their properties, and their applications is crucial for anyone studying material science or engineering.
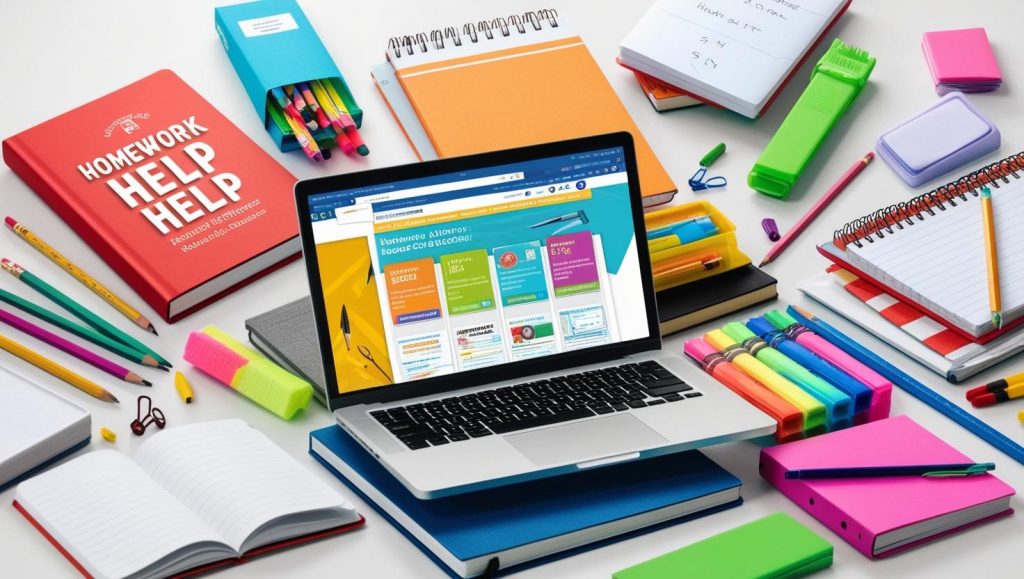
In this blog, we will explore the fundamental concepts behind composite materials, their types, and the mathematical principles that govern their behavior. Whether you’re tackling homework assignments, preparing for exams, or exploring the subject further, this comprehensive guide provides you with everything you need to know.
What Are Composite Materials?
Composite materials are created by combining two or more distinct materials with different physical or chemical properties. The resulting material often has characteristics that make it more versatile, durable, or cost-effective than the individual components. The primary components in composite materials are:
- Matrix: The continuous phase that holds the reinforcement material in place.
- Reinforcement: The material embedded within the matrix to enhance the mechanical properties of the composite (e.g., fibers, particles).
By carefully selecting and combining these components, engineers can design composite materials with tailored properties to meet specific needs. The use of composite materials has increased in industries where strength, light weight, and durability are paramount.
Types of Composite Materials
Composite materials come in various types, depending on the arrangement of the reinforcing phase and the matrix. Let’s explore the most common types.
1. Fiber-Reinforced Composites
These are the most common and widely used composites, especially in aerospace, automotive, and construction industries. The reinforcing phase typically consists of fibers such as carbon fibers, glass fibers, or aramid fibers. The matrix can be a polymer, metal, or ceramic.
Advantages:
- High strength-to-weight ratio
- Excellent fatigue resistance
- High durability
Example: Carbon Fiber-Reinforced Polymer (CFRP) is a popular material in the aerospace industry due to its strength and lightness.
External Link: Fiber-Reinforced Composites Overview – Composites World
2. Particle-Reinforced Composites
In particle-reinforced composites, the reinforcement is in the form of small particles or flakes. These composites are often used in applications where enhanced thermal or electrical conductivity is required.
Advantages:
- Improved wear resistance
- Increased strength at high temperatures
Example: Concrete is a common example of a particle-reinforced composite, where aggregate particles are embedded in a cement matrix.
3. Laminated Composites
Laminated composites are made by stacking multiple layers of composite materials, which can be of different types. These layers are bonded together using adhesives or resins, resulting in a material with properties tailored for specific applications.
Advantages:
- Customizable mechanical properties in multiple directions
- Can be used in structures that require high impact resistance
Example: Plywood is a simple form of laminated composite material used in construction.
External Link: Laminated Composites – Properties and Applications
Key Properties of Composite Materials
Understanding the properties of composite materials is essential for solving homework problems and applying them to real-world situations. Here are the key properties that determine how composites perform:
1. Mechanical Properties
Mechanical properties such as tensile strength, compressive strength, and elastic modulus are crucial when evaluating composite materials for structural applications. The behavior of a composite material under stress depends on the combination of the matrix and reinforcement materials.
Example Question:
Given a fiber-reinforced composite with a matrix modulus of 5 GPa and fiber modulus of 200 GPa, and 30% fiber volume fraction, calculate the effective modulus of the composite.
Solution:
The effective modulus EcE_cEc for a fiber-reinforced composite can be calculated using the rule of mixtures: Ec=Vf⋅Ef+Vm⋅EmE_c = V_f \cdot E_f + V_m \cdot E_mEc=Vf⋅Ef+Vm⋅Em
Where:
- EfE_fEf = fiber modulus
- EmE_mEm = matrix modulus
- VfV_fVf = fiber volume fraction
- VmV_mVm = matrix volume fraction (1 – VfV_fVf)
Substitute the values: Ec=(0.3⋅200)+(0.7⋅5)=60+3.5=63.5 GPaE_c = (0.3 \cdot 200) + (0.7 \cdot 5) = 60 + 3.5 = 63.5 \, \text{GPa}Ec=(0.3⋅200)+(0.7⋅5)=60+3.5=63.5GPa
2. Thermal Properties
Composites can also be designed to have specific thermal properties, such as thermal conductivity, thermal expansion, and heat resistance. These properties are essential for applications in aerospace, electronics, and high-temperature environments.
Example Question:
How does the coefficient of thermal expansion (CTE) of a composite material behave when the matrix has a CTE of 12×10−6 °C−112 \times 10^{-6} \, \text{°C}^{-1}12×10−6°C−1 and the reinforcement has a CTE of 5×10−6 °C−15 \times 10^{-6} \, \text{°C}^{-1}5×10−6°C−1, with a 40% reinforcement volume fraction?
Solution:
The CTE of the composite can be estimated by using the rule of mixtures for thermal expansion: CTEc=Vf⋅CTEf+Vm⋅CTEm\text{CTE}_c = V_f \cdot \text{CTE}_f + V_m \cdot \text{CTE}_mCTEc=Vf⋅CTEf+Vm⋅CTEm
Where:
- CTEf\text{CTE}_fCTEf = CTE of the reinforcement
- CTEm\text{CTE}_mCTEm = CTE of the matrix
Substituting the values: CTEc=(0.4⋅5×10−6)+(0.6⋅12×10−6)=2×10−6+7.2×10−6=9.2×10−6 °C−1\text{CTE}_c = (0.4 \cdot 5 \times 10^{-6}) + (0.6 \cdot 12 \times 10^{-6}) = 2 \times 10^{-6} + 7.2 \times 10^{-6} = 9.2 \times 10^{-6} \, \text{°C}^{-1}CTEc=(0.4⋅5×10−6)+(0.6⋅12×10−6)=2×10−6+7.2×10−6=9.2×10−6°C−1
External Link: Thermal Properties of Composites
Applications of Composite Materials
The versatility of composite materials makes them applicable in various industries. Let’s explore some common applications:
1. Aerospace Industry
Composite materials are used extensively in aerospace applications due to their high strength-to-weight ratio and durability. For example, carbon fiber and titanium composites are often used in aircraft structures, reducing weight and improving fuel efficiency.
External Link: Aerospace Composites – A Brief Overview
2. Automotive Industry
In the automotive industry, composite materials are used to manufacture lightweight components, such as body panels, bumpers, and interior parts, improving fuel efficiency and performance. Materials like fiber-reinforced polymers are common in this sector.
3. Construction Industry
Composites are also widely used in construction, especially for making reinforced concrete, fiber-reinforced polymers for building materials, and carbon fiber-reinforced concrete for enhanced durability in bridges and other structures.
Conclusion: Mastering Composite Materials in Homework
Composite materials are integral to many of today’s most advanced technologies, from aircraft and automobiles to construction and sports equipment. By understanding the fundamental concepts, types, properties, and applications of composite materials, you will be well-equipped to tackle your Composite Material Homework Help with confidence. Whether it’s performing calculations for strength, thermal properties, or understanding the real-world applications of composites, the key to success lies in grasping the underlying principles of composite behavior.